Qu'est-ce que la méthode AMDEC et comment l'utiliser ?
Cet article explique ce qu'est la méthode AMDEC (c'est-à-dire l’Analyse des Modes de Défaillance, de leurs Effets et de leur Criticité).
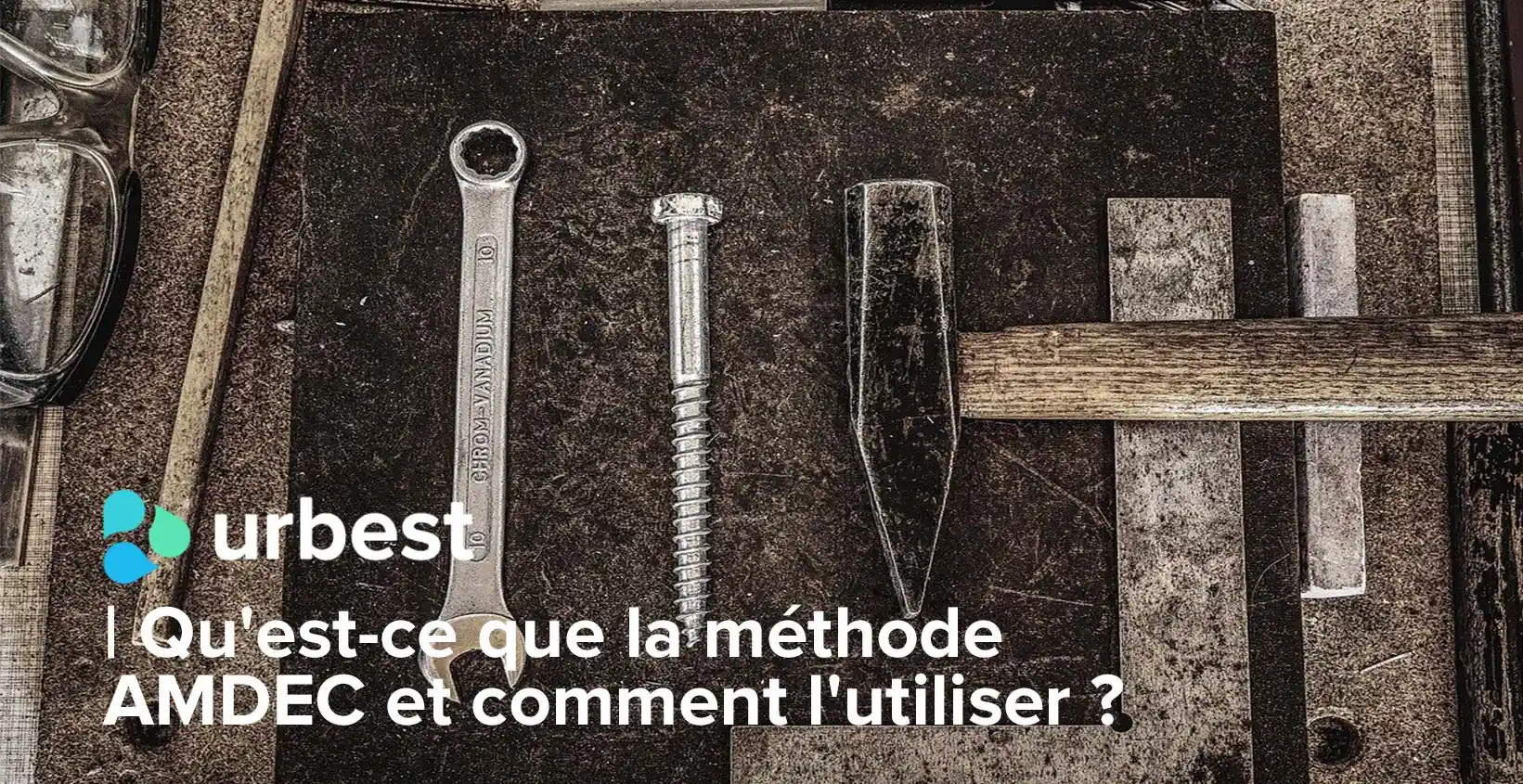
Cet article explique ce qu'est la méthode AMDEC (c'est-à-dire l’Analyse des Modes de Défaillance, de leurs Effets et de leur Criticité). Cette analyse des processus peut être un outil puissant dans de nombreux plans de maintenance, de travaux à effectuer ou simplement d’une démarche d’amélioration continue..
L'AMDEC est une méthode qui guidera les personnes à définir des actions correctives. Que signifie AMDEC ? Comment fonctionne la méthode AMDEC ? Comment utiliser cette méthode et la mettre en œuvre dans mon entreprise ?
Il ne faudra pas beaucoup de temps pour répondre à ces questions.
Avant de commencer à répondre à ces questions, nous devons revenir un peu en arrière et parler de l'outil original d'analyse de la fiabilité de la maintenance appelé AMDE.
L'AMDE est l'acronyme de l'Analyse des Modes de Défaillance et de leurs Effets et représente une approche étape par étape que l'on peut adopter pour identifier toutes les défaillances possibles dans une conception, un produit, un processus ou un service (=> analyse des modes de défaillance) et évaluer les effets possibles de ces défaillances (=> analyse des effets).
L'AMDE aide à déterminer les actions à mettre en place pour atténuer certains risques liés à la défaillance d'un système.
Dans les processus et produits complexes, trouver et améliorer les maillons les plus faibles est plus facile à dire qu'à faire.
Bien que l'exécution soit similaire, certains détails différencient la façon dont une personne aborde l'identification des défaillances de conception par rapport aux défaillances de processus, c'est pourquoi l'AMDE est divisée en différentes catégories comme l'AMDEC production et l'AMDEC processus.
Elles sont étroitement liées l'une à l'autre car l'une identifie le risque dans le produit et la seconde identifie le risque dans le processus de production (ou fabrication).
Qu'est-ce que l'AMDEC ?
AMDEC (PFMEA en Anglais) est l'abréviation de Analyse des modes de défaillance, de leurs effets et de leur criticitéL'AMDEC se concentre sur les processus. Il s'agit d'un outil qualitatif, d'un document vivant, qui fait un zoom sur les processus actuels pour identifier les points d'amélioration.
Une AMDEC décompose votre processus de maintenance en ses différentes étapes et les examine méthodiquement à la recherche de risques ou de défaillances potentiels.
Cette approche peut être utilisée dans de nombreux scénarios différents :
- Avant l'élaboration de plans de contrôle pour un process nouveau ou modifié
- Lors de l'introduction d'un nouveau processus, d'une nouvelle méthode, d'une nouvelle exigence ou d'une nouvelle technologie
- Lorsqu'un processus existant doit être amélioré
- Lorsqu'il y a une nouvelle façon de mettre en œuvre un processus existant
- Pendant l'exécution et la gestion du processus pour les mesures de contrôle de la qualité.
- Lors de la relocalisation d'un processus dans une nouvelle installation.
L'AMDEC évalue chaque étapes du processus et son effet afin d'attribuer une note sur une échelle de 1 à 10 pour les variables suivantes :
- Gravité - évalué l'impact du mode de défaillance (l'erreur dans le processus), 1 représentant le problème de sécurité le moins grave et 10 le problème de sécurité le plus dangereux.
On peut également utiliser un critère financier en termes de coûts si un événement se produit ou un critère environnemental pour juger de la criticité en cas de survenue d'un événement. Dans la plupart des cas, les processus dont le score de gravité dépasse 8 peuvent nécessiter une analyse par arbre de défaillance, qui estime la probabilité du mode de défaillance en le décomposant en sous-éléments supplémentaires.
- Occurrence - évalue la probabilité qu'une défaillance se produise, 1 représentant l'occurrence la plus faible et 10 l'occurrence la plus élevée. Par exemple, un score de 1 peut être attribué à une défaillance qui se produit une fois tous les 5 ans, tandis qu'un score de 10 peut être attribué à une défaillance qui se produit une fois par heure, une fois par minute, etc.
- Détection - évalue la probabilité qu'une défaillance soit détectée, 1 représentant la probabilité la plus élevée de détection et 10 la probabilité la plus faible de détection.
Formule pour calculer l’Indice de Priorité du Risque
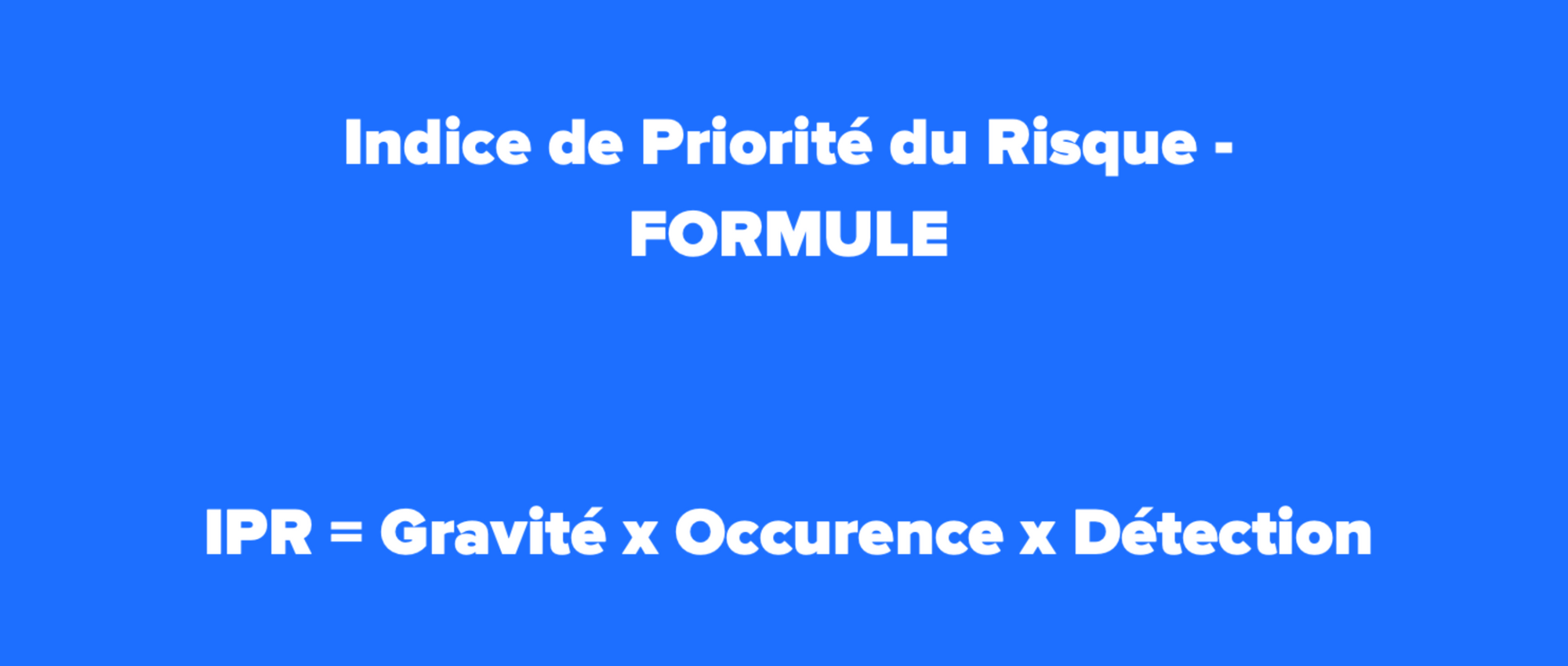
En règle générale, toute valeur d'IPR supérieure à 80 nécessite une action corrective.
L'action corrective conduira idéalement à un IPR inférieur.
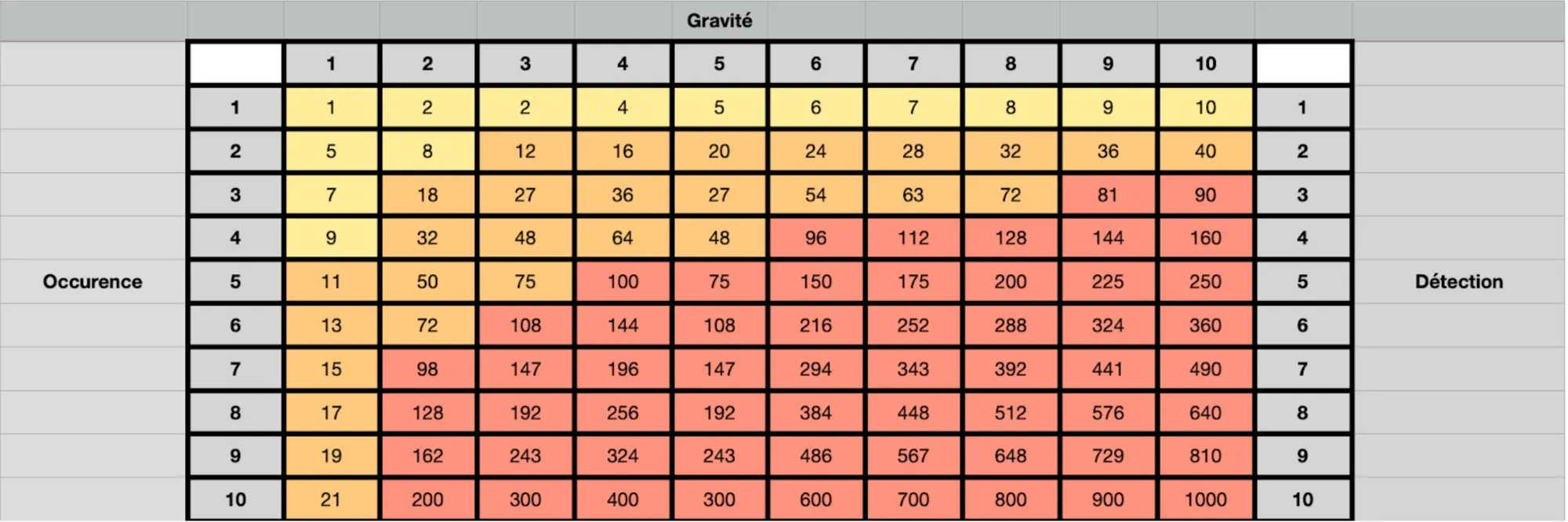
Quelles sont les étapes du processus à évaluer ?
Étape 1 | Examiner le processus
Utilisez un organigramme du processus pour identifier chaque composant du processus. Identifiez le processus et les étapes intermédiaires à l'aide d'un diagramme détaillé.
Identifiez ce que chaque étape est censée accomplir.
Étape 2 | Reflexion sur les modes de défaillance potentiels
Examinez la documentation et les données existantes pour trouver des indices sur les causes.
Étape 3 | Dressez la liste des effets potentiels de la défaillance
Il peut y en avoir plus d'un pour chaque défaillance.
Étape 4 | Attribuer une note pour chaque degré de gravité
Les classements de gravité sont basés sur la gravité des conséquences de la défaillance : 1 (faible risque) - 10 (dangereux).
Étape 5 | Attribuer des classements d'occurrence
Les classements d'occurrence sont basés sur la fréquence à laquelle la/les causes de la défaillance est susceptible de se produire : 1 (moins probable) - 10 (extrêmement probable).
Étape 6 | Attribution des classements de détection
Basé sur les chances que la défaillance soit détectée avant que le client ne la trouve : 1 (détection facile) - 10 (extrêmement difficile à détecter).
Étape 7 | Calculer l'IPR
Déterminez si le nombre calculé est acceptable pour la défaillance analysée.
IPR = Gravité X Occurrence X Détection.
Étape 8 | Élaborer le plan d'action
Définissez qui fera quoi, quand, à quel moment et quel moyen utilisé, avec Urbest.
Etape 9 | Prendre des mesures et mettre en œuvre les améliorations identifiées par votre équipe AMDEC.
Par exemple: Remplacer le produit, formation à l’utilisation du produit pour les employés ou du client…
Etape 10 | Calculer l'IPR résultant
Réévaluez chacune des défaillances potentielles une fois les améliorations apportées et déterminez l'impact de ces dernières.
Maintenant que nous connaissons toutes les clés de l'AMDEC, voici 6 actions pour parvenir à mettre votre méthode en place:
1_ Créez un groupe de travail spécifique pour mener à bien le processus. L'AMDEC ne doit pas se faire en solo.Si cela est possible, ce type d'analyse doit être réalisé par une équipe multidisciplinaire. Parfois, dans une petite entreprise, les employés ont plusieurs rôles.
Nombreux sont les entrepreneurs qui ont la fonction de PDG, de directeur financier, d'ingénieur de conception, de responsable de l'analyse et de l'assurance qualité. L'idéal est d'adopter une approche d'équipe si possible. Faites participer à cette analyse le personnel de direction qui est responsable de la gestion des process.
2_ Définissez les objectifs de ce projet. (conseil : faites en sorte qu'ils soient aussi définitifs qu'il est raisonnablement possible de le faire).
3_ Déterminez les étapes à réaliser.
4_ Calculez les IPR de tous les processus qui méritent d'être évalués.
5_ Assignez les tâches du processus à chaque membre de l'équipe.
*Si ces tâches ne découlent pas de vos objectifs et de votre carte des processus, c'est le moment d'apporter des modifications à vos documents de base avant d'aller plus loin.
6_ Suivez les tâches et le calendrier.
Malgré leurs nombreux avantages, les AMDEC ne résoudront pas toutes les défaillances. Si c'était le cas, les responsables de la maintenance et les ingénieurs en fiabilité n'auraient jamais à se concentrer sur les mesures des défaillances.
Les types de défaillances identifiées et les solutions associées sont étroitement liés à l'expérience et à la qualité des connaissances ou de la formation de l'équipe pluridisciplinaire chargée de mener le processus et à son accès aux enregistrements historiques.
L'un des meilleurs moyen de recueillir des données historiques est d'utiliser des outils collaboratifs comme Urbest qui vous permettront d’enregistrer des données sur tout le processus d’un problème.
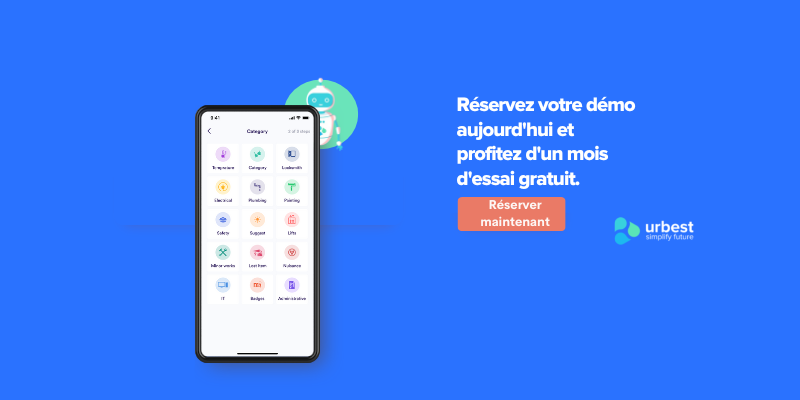
L’étude des données vous permettra de définir les causes et les actions correctives nécessaires, depuis la formulation de la demande, jusqu'à la satisfaction du client final.
Si vous pouvez supporter une courbe d'apprentissage un peu raide, l'AMDEC est un outil d'évaluation des risques inestimable qui peut avoir un impact important sur votre management, votre travail, vos résultats et la formation de vos équipes.