How Maintenance moved from curative to preventive?
Experiencing a failure at work is almost inevitable for most asset-intensive organisations. This is why deploying a maintenance strategy is key to keeping critical assets available at all times.
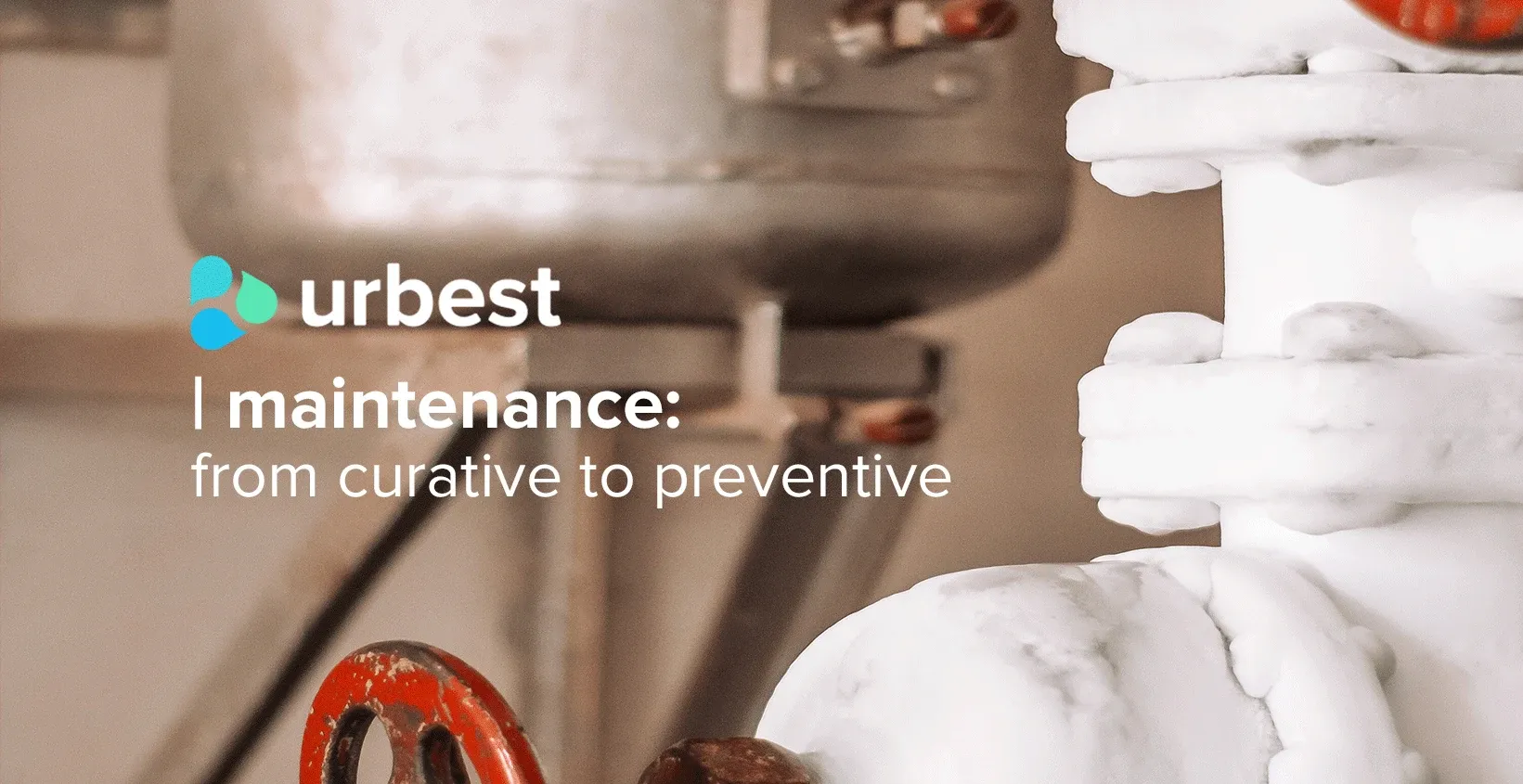
Experiencing a failure at work is almost inevitable for most asset-intensive organisations. This is why deploying a maintenance strategy is key to keeping critical assets available at all times.
Understanding what curative maintenance is:
Let's start from the basics, what is curative maintenance? Curative maintenance (also called reactive maintenance) is when a machine or an installation has broken down requiring to replace the equipment partially or in its entirety. In other words, the curative maintenance can be considered as sudden repair of defective or damaged equipment.
From a work perspective, curative maintenance seems appealing to some fleet managers because it only addresses problems when they occur. Yet there are two serious problems associated with this particular approach. First of all, the breakdowns interrupt the regular workflow, it affects your service and people who need your service. In addition, unplanned maintenance will put you in last minute mode which will cost you more if you need a supplier in the hour. It will also affect your timescale and other things planned in your diary because these other tasks will be delayed.
Curative maintenance is not entirely avoidable, but much of it can be prevented.
So what is preventive maintenance?
Preventive maintenance is maintenance that is regularly performed to lessen the likelihood of failing. Maintenance is performed while an asset is still working so that it does not break down unexpectedly. For example, an equipment can be maintained in anticipation to avoid nuisance caused by accumulation of dust in the filtering system.
Good preventive maintenance is all about planning and finding the fine-tuning of frequencies that you need to have with your product/equipment/asset. For this, there's an easy way to own your maintenance schedule: just follow the PDCA model (Plan, Do, Check and Act).
How maintenance moved from curative to preventive?
In order to understand how one can transition from curative to preventive one need to understand benefits of working in a preventive way. Research on preventive maintenance shows reduced unplanned downtime, fewer breakdowns of equipment and essential machinery, increased reliability of critical assets. Most importantly, there will simply be fewer expensive corrective and emergency repairs. And for the bottom line, preventive can reduce your costs significantly.
According to Comparesoft, there are also disadvantages to preventive maintenance such as the possibility of excessive preventive maintenance, the High start-up and implementation costs and the need for more resources (spare parts, staff, etc.) or time.
Which maintenance should you choose?
An analysis of your organization is necessary, in order to choose wisely between the different types of maintenance and to optimize the management of breakdowns of your machines:
- Maintenance according to your objectives: cost reduction, asset availability, audits, asset durability, work environment safety
- The technical capacity available: automated intervention, remote intervention (or remote maintenance) with the help of technical support (telephone, chat, etc.), physical intervention, assisted intervention management software (CMMS) such as Urbest
- The desired purpose:
- to prevent breakdowns → preventive maintenance
- to repair equipment → curative maintenance
- to analyze the equipment → predictive maintenance
- The nature of your installations also affects the expected quality of your services and tolerance for breakdowns. If customer service expectations are not too high, it can sometimes be more financially beneficial to tolerate the occurrence of an outage and correct it.
In the words of TWI, it is essential to consider the needs to choose from these different types of maintenance according to your type of asset or building, its security / services issues and the level of training of your teams. Predictive maintenance, for example, is more complex to implement and its daily use requires certain prerequisites.
In addition, your maintenance can be boosted by a CMMS (computerised management maintenance system); the somewhat obsolete term includes digital tools allowing better monitoring of maintenance actions which can now be done in a collaborative way.
Using a CMMS provides task and work tracking, lists parts and equipment, saves precious time, and does not require extensive training to get started if you take a platform like Urbest. There are several types, in different forms; so don't hesitate to rely on such systems to apply your maintenance: it's a safe bet that you will find the ideal recipe for your business.
Reality shows that regular control and preventative maintenance can’t fix all potential maintenance problems. There will still be an occasional unexpected breakdown, but it also shows that prevention can help address problems before they turn into serious breakdowns.
While a corrective maintenance strategy may remain used, a balance between preventive and corrective maintenance is today highly recommended for companies, making even possible to move towards predictive maintenance in the near future and make your life easier.
You could also read:
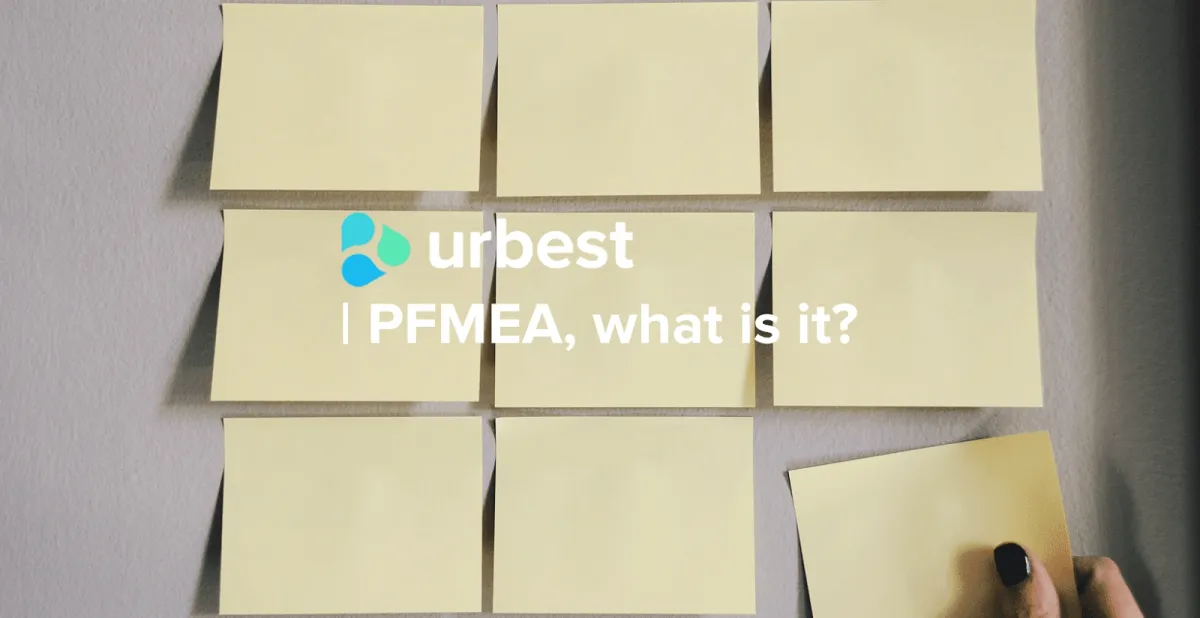
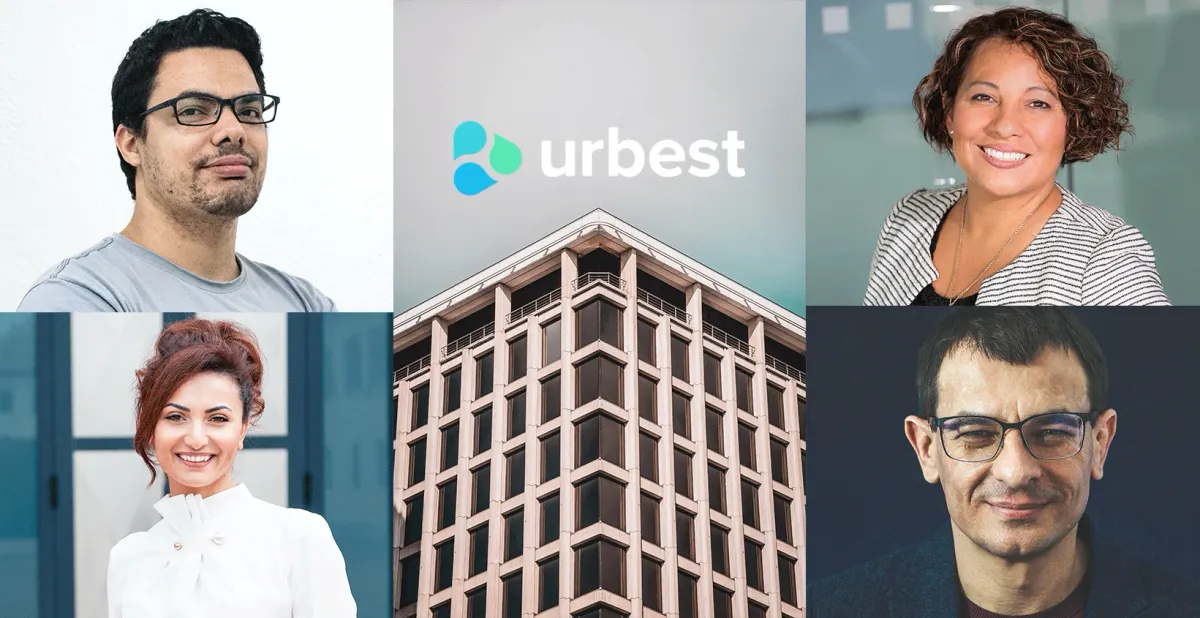