Maintenance Strategies: Which One Best Suits Your Business Needs
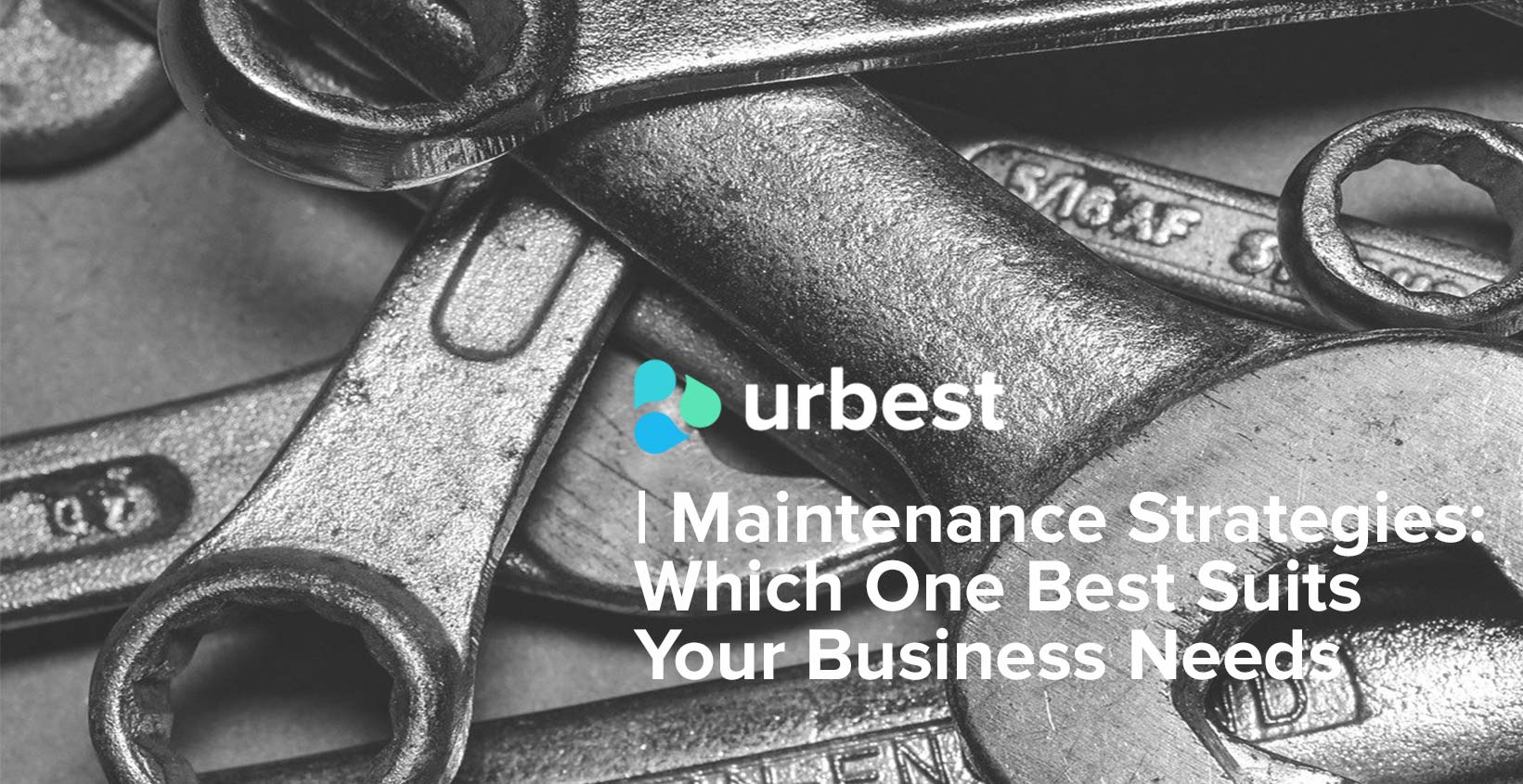
If your business involves the property or facility management, be it for offices, residential units or for commercial purposes, you are no doubt aware that a considerable amount of your overhead is consecrated to the maintenance and upkeep of the property, its equipment, and facilities. Furthermore, well-kept property goes a long way toward improving customer satisfaction. It plays, thus, a significant role in your business’s bottom line.
Whether you’re a small business with one or few properties, or a larger enterprise managing an extensive portfolio of assets and are looking to implement a reliability-centered maintenance strategy (RCM), you must be able to foresee future costs, evaluate the cost to benefit ratio, and stay organized to maximize the flow of information and minimize downtime and any nuisance incurred to your clients or tenants.
In this article, we will take a brief look at the various types of maintenance strategies implemented in the property management sector and examine their pros and cons.
Is it essential to plan for maintenance?
Some companies (usually smaller companies or those more focused on short-term goals) might take an ‘as-needed’ approach to maintenance also called reactive maintenance or “run-to-fail”. However, if you are running more complex facilities, have ambitions of expanding, or have set your sights on the long term, there are distinct advantages to planning for maintenance:
- Prevent the premature break down of equipment or structures
- Reduce expenses by maximizing the efficiency of equipment or structures
- Improve the value of an asset
- Save money by avoiding emergency repairs
If these benefits appeal to you, perhaps the maintenance strategy best suited for your needs is what’s called, Preventive Maintenance.
Preventive maintenance involves the regular repairs of equipment, structures, and facilities even when they are functioning more or less correctly.
Preventive Maintenance allows you to:
- Keep budget to a predictable level
- Reduce or eliminate extended and inconvenient downtime
- Reduce the time and costs involved in controls and monitoring of your assets
Preventive Maintenance can be divided into two distinct categories: Time-Based Maintenance and Usage-Based Maintenance.
In property management, a time-based maintenance strategy is by far the more common of the two types of Preventive Maintenance methods. However, if you manage assets that do not adhere to regular or seasonal usage patterns, then perhaps a usage-based maintenance schedule would make more sense.
Is Preventive Maintenance the Right Strategy for You?
In most property management or building maintenance operations, the failure or depreciation of equipment, or the structures themselves, is due to usage which follows regular or seasonal patterns. This is why Preventive Maintenance is so popular in the building management sector. However, it may not be the right strategy for you if equipment failure or property damage frequently occurs in ways that are not based solely on regular and normal usage.
In most rental contracts there are clauses that place the cost and burden of repairs due to reasons beyond regular and normal usage upon the tenant. Additionally, you may have an insurance provider that will assume the cost of repairs due to unforeseen events.
If you find a majority of your maintenance surrounds unpredictable usage, it wouldn’t make sense to carry out a strategy of Preventive Maintenance.
After all, how can we prevent what is unforeseeable or what is beyond our control?
It would require a sizeable amount of data points covering a relatively large amount of time to determine whether these unforeseeable events occur at a high enough rate to make Preventive Maintenance not worth implementing.
This type of calculation can best be determined with an effective facility management program.
Is Reactive Maintenance the Right Strategy for You?
Reactive maintenance (also called ‘Run to Fail’) involves carrying out repairs or maintenance activities only when equipment stops functioning or when severe damage to property or facility occurs.
Reactive maintenance is generally regarded as a short-sighted approach. The repairs, due to their emergency nature, could cost you significantly more according to RICS table for upholding professional standards. Because the downtime involved with reactive repairs is not planned for, it is quite possible, and often the case, that the repairs come with a considerable amount of nuisance or inconvenience to the tenant.
This kind of strategy also frequently leads to a shorter asset life expectancy.
However, there is a time and a place for Reactive Maintenance:
- If the cost of Preventive Maintenance is considered as high
- If you are operating an asset in end of life
- If the occupier of the buildings can cope with regular negative impacts
- If your priority is to increase short-term cash flows
More often than not, property management professionals rely on a combination of Preventive and Reactive Maintenance. IBM suggests common ratio is 70% Preventive to 30% Reactive.
Finding the ratio that best suits your needs will require a careful analysis of costs, projected earnings, maintenance needs, and frequency, as well as a host of other factors. To define the most effective balance between Preventive and Reactive Maintenance strategies, there is no substitute for a comprehensive and coherent facility management program.
Is Predictive Maintenance the Right Strategy for You?
Predictive maintenance is a condition-based maintenance strategy saying that maintenance should be carried out when certain indicators reveal signs of decreasing performance or impending failures.
Predictive maintenance is a method based on condition-monitoring tools and techniques that track the performance of equipment under normal operating conditions to determine likely defects or dips in performance and fix them before they turn into failures.
Predictive Maintenance is similar to Preventive Maintenance in that it is carried out in regular intervals over a predetermined (usually lengthy or continuous) period. However, Predictive Maintenance favors monitoring over regular interventions.
A key component to Predictive Maintenance is IoT devices which provide data, alerts, analyses, and identifies areas that require attention.
Predictive Maintenance is commonly regarded as a more cost-effective strategy than Preventive Maintenance or Reactive Maintenance. Used correctly, Predictive Maintenance allows you to:
- Minimize the inconvenience and downtime associated with repairs
- Minimize the costs associated with repairs (material and labor)
- Optimize the energy efficiency of equipment and intervene only when it is advantageous
However, implementing an effective Predictive Maintenance Strategy often requires a relatively high level of technical expertise. And some of the monitoring tools may cost more than they are worth to you.
To determine whether Predictive Maintenance is the right strategy for you, a few factors need to be taken into consideration:
- Level of technical expertise at your disposal
- Cost to replace vs. cost to repair
- Frequency of failure due to non-regular or uncommon usage
Predictive Maintenance strategies can often get highly technical and precise. They involve monitoring data to assess risks associated with pertinent issues and then prioritizing corrective actions. FMECA (Failure Modes, Effects and Criticality Analysis) aims to identify potential failures, assess the risks associated with those failures, rank the issues in terms of importance then identify and carry out corrective actions.
Collecting and analyzing the relevant data to implement such a solution requires a powerful, well-designed facility management program.
There are facility management programs on the market that are better suited for a Predictive Maintenance strategy than others. Some factors worth considering when choosing the right program for a successful Predictive Maintenance strategy are:
- How user-friendly is the facility management program?
- How flexible is the facility management program?
If the facility management program you are using is overly complex or overly rigid in its design and implementation, then getting any practical function out of the data points collected in a Predictive Maintenance strategy will be near impossible.
For more information on high-performance, user-friendly facility management programs that work effectively with a Predictive Maintenance strategy click here.
A Comprehensive Building Maintenance Strategy
While Preventive Maintenance, Reactive Maintenance, and Predictive Maintenance each has its advantages and disadvantages, to optimize the value of your asset and reduce costs, downtimes and inconveniences a combination of the three methods will prove most effective.
Maintenance Strategies Compared

Defining and implementing the appropriate maintenance strategy for your business, i.e., the most effective and efficient ratio of the three above methods will require you to gather, analyze and share relevant data in an organized and coherent fashion. Thus, the first, and perhaps the most important, step is to select the facility management program that is best adapted to your business and your needs.
If you are not yet using a facility management program, or if the one you are currently using is not meeting your expectations, the good news is that there is a powerful, user-friendly, facility management that can help you along your growth; and you can try it out for free!
You can also be interested in:

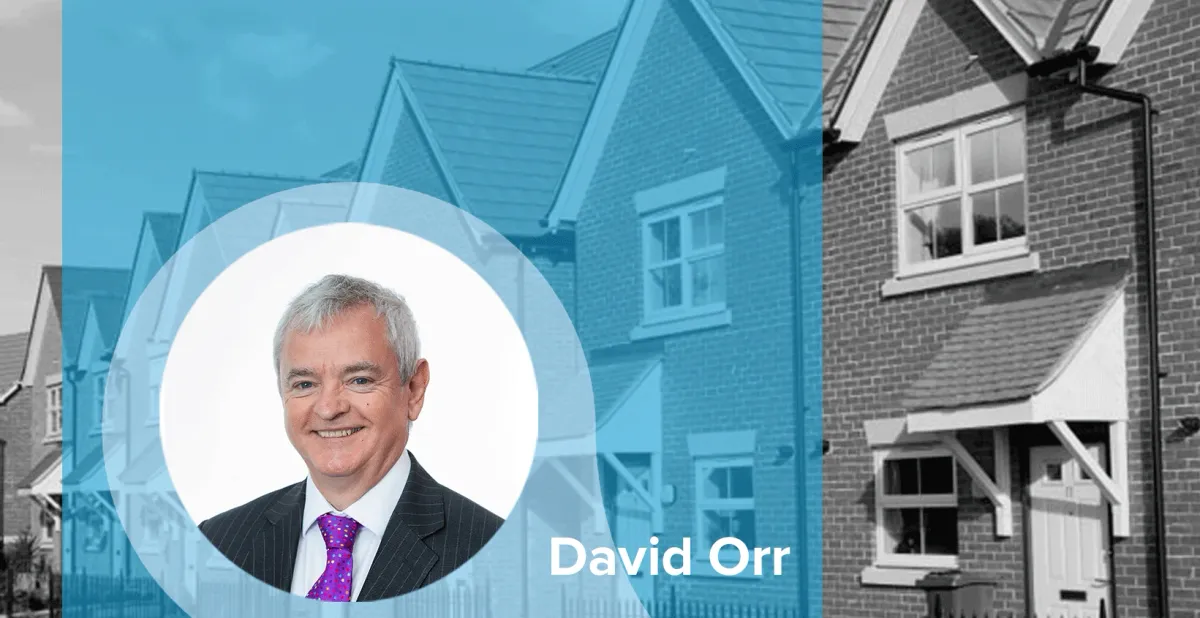