How to set up your predictive maintenance plan
Predictive maintenance is becoming increasingly popular with maintenance companies.
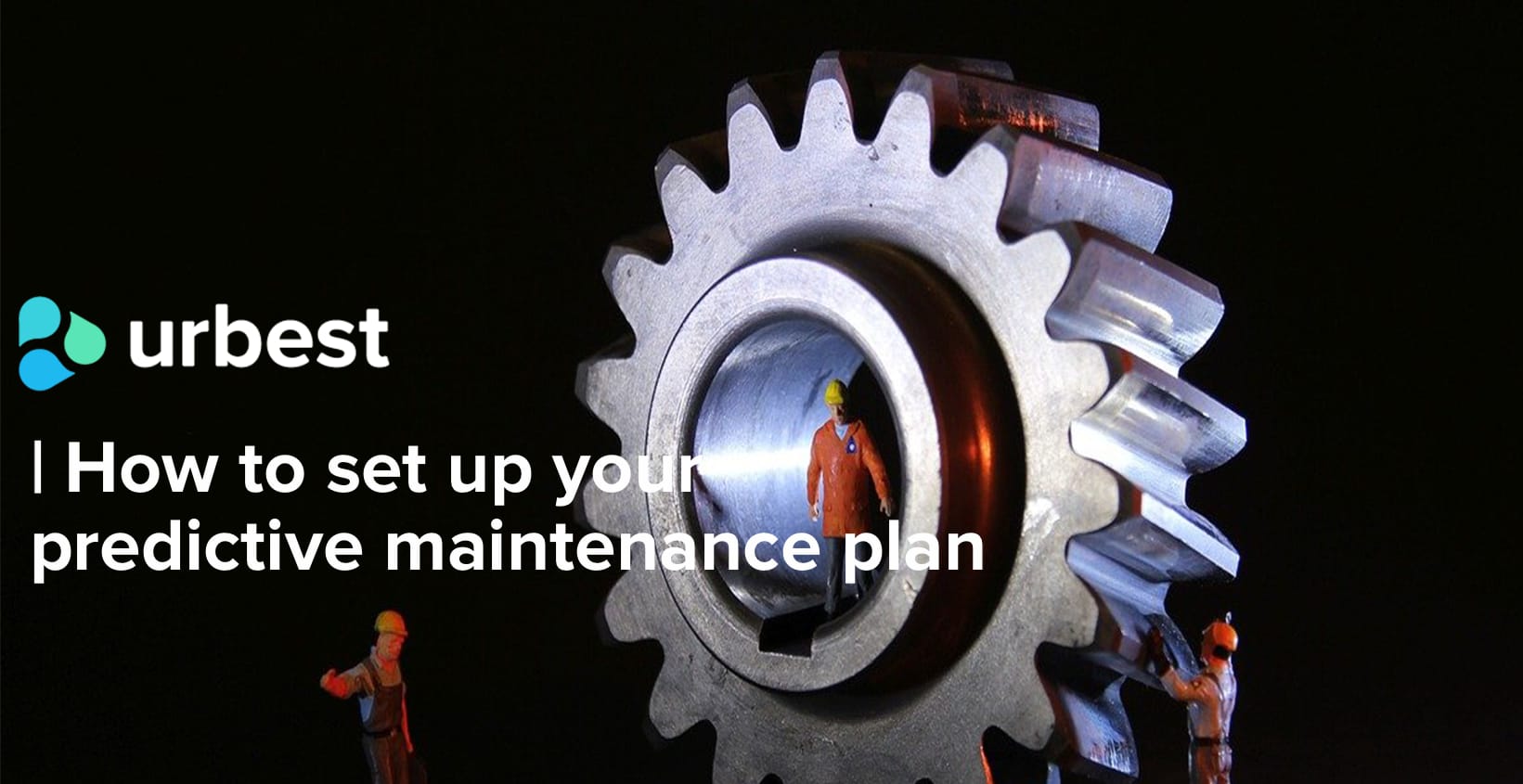
Predictive maintenance is becoming increasingly popular with maintenance companies.Indeed, when it is well carried out, it makes it possible to avoid the immobilisation of equipment with the resulting loss of time and financial repercussions. The subtlety is to succeed in intervening just when it is necessary thanks to the help of signals that will indicate the warning signs of a breakdown or a malfunction.
To do this, it is essential to create decision rules and to send up alerts or alarms to prepare for the detection of anomalies.This article reviews the benefits of predictive maintenance and how it can be implemented.
1 - How to detect breakdowns before they happen?
Are you able to anticipate equipment breakdowns or malfunctions? Do you have the necessary tools to collect the data that will allow you to anticipate breakdowns?
Two solutions are available to you in order to capture and exploit this type of data:
- The first solution is to exploit previous data.
Indeed, if your company has been in existence for several years, you should have historical data concerning the breakdowns of your equipment over time.
By exploiting these indicators such as MTBF you will be able to know the frequency of equipment failures and have an indication of the timing of future failures.
However, this mode of operation has its limits... Indeed, if some equipment never breaks down or at intervals that are not regular, it will be difficult to predict the dates of its next anomalies. Equipment can also malfunction without being stopped or broken down. These malfunctions can have a significant impact on energy consumption and the quality of service provided (comfort, air quality, etc.).
- A more modern solution is to connect to the equipment directly.
In practice, connected sensors can be used to connect to the equipment, or in some cases, it is possible to connect directly to the equipment's automatic controls.The data collected in this way can be used to find out about wear and tear, time in use, or deviation from expected performance (e.g. temperature sensor or CO2 readings).
Knowing the weak signs will allow you to replace or avoid a total shutdown of the equipment and to quickly correct any malfunctions that may occur.Algorithms are also able to compile this data in order to prepare actions and tell you which equipment or parts to replace.
These algorithms can also send the tasks to be carried out directly to an application such as Urbest in order to gain reactivity and warn the maintenance department concerned or trigger the ordering of the part.
2 - How a job tracking application can help you with your preventive maintenance plan.
The second step in your maintenance plan is to organise your teams to work as efficiently as possible.The time saved on avoided downtime and on the rapid correction of equipment malfunctions should not be lost through poor management of interventions.
Task management and tracking application such as Urbest will help you to structure this second part.
The data from your software or that you enter manually into the application will automatically create tasks to be carried out. These tasks can be assigned directly to the right person.
These tasks contain :
- A description of the request
- The location of the request
- A picture of the equipment
- The type of operation to be performed
- The person in charge
- The deadline for processing the request.
The simplicity of collaborative software such as Urbest compared to a CMMS allows you to be reactive, mobile, and to access the right information quickly.The software will also help you to analyse intervention data, which will enable you to flesh out your algorithm for the preventive maintenance plan.
As soon as a task is created, the assigned employee receives an instant notification with all the details of the operation he/she has to perform.
Predictive maintenance will probably become the most used maintenance in the next few years. By implementing sensors (or connecting to existing sensors) and processing the associated data, you will be able to implement your preventive maintenance plan.
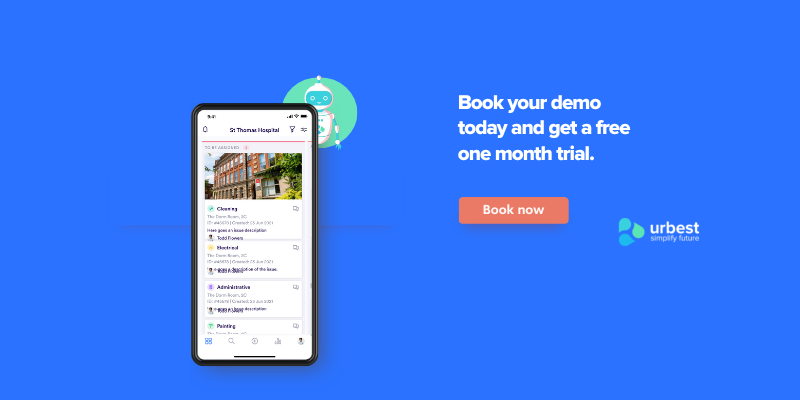
To receive the latest news and articles on innovations in maintenance and facility management, subscribe to our newsletter.