Les 8 Piliers du TPM : La Maintenance Productive Totale pour une Meilleure Performance
La Maintenance Productive Totale (TPM) est une méthode de gestion de la maintenance des équipements, visant à améliorer la productivité, la qualité et l'efficacité des processus de production.
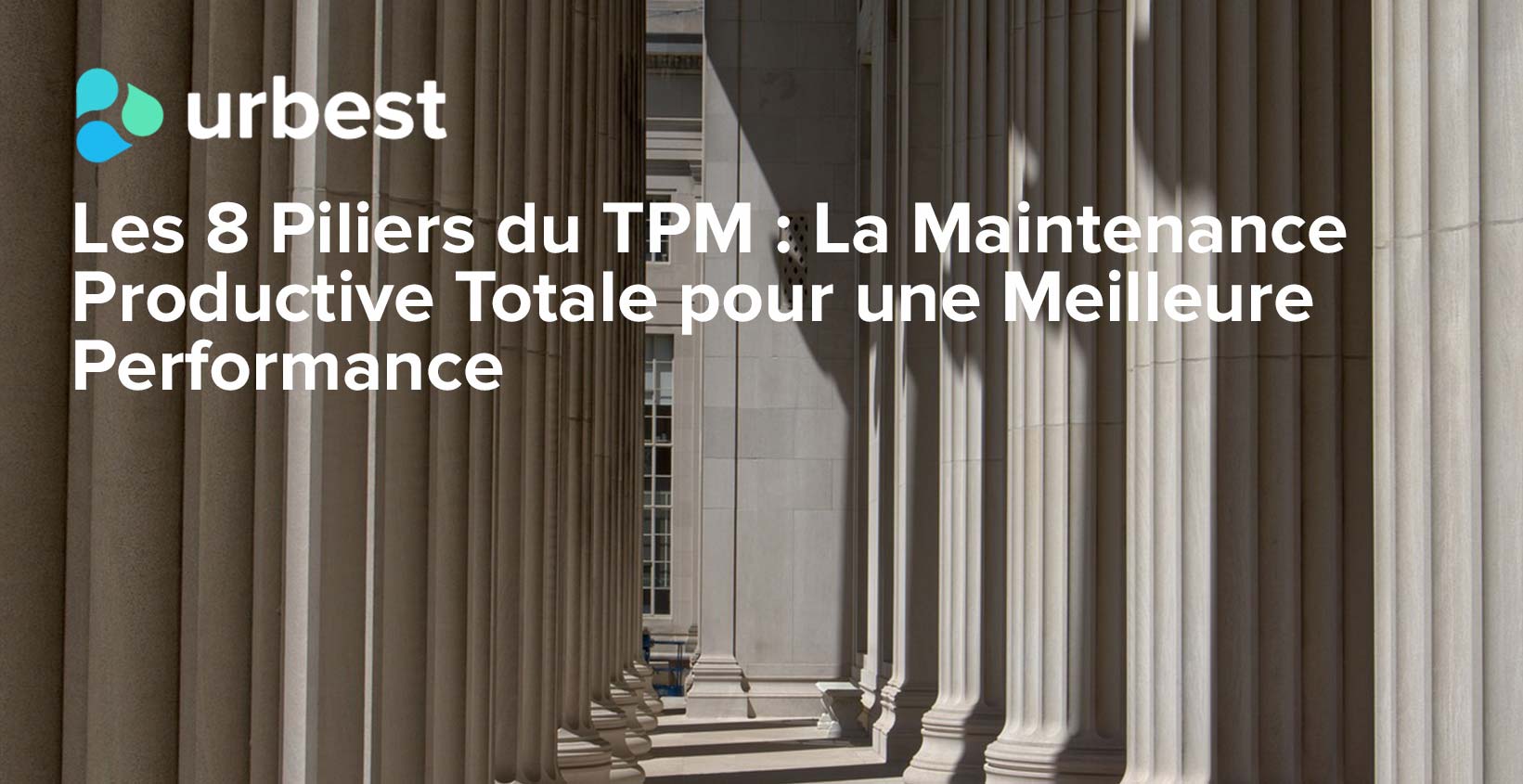
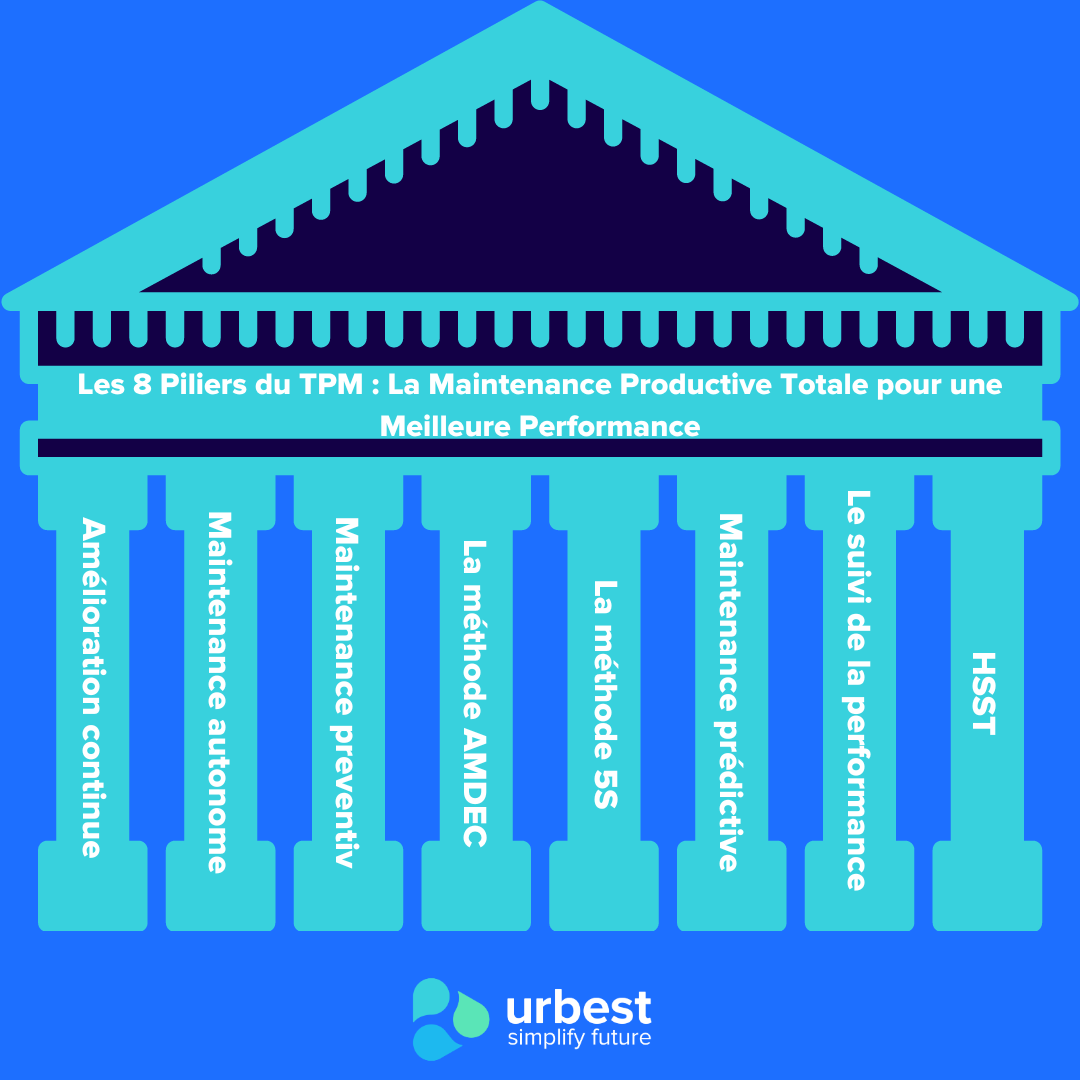
Introduction à la Maintenance Productive Totale (TPM)
La Maintenance Productive Totale (TPM) est une méthode de gestion de la maintenance des équipements, visant à améliorer la productivité, la qualité et l'efficacité des processus de production.
Le concept de TPM est basé sur 8 piliers qui permettent d'optimiser la maintenance des équipements et d'assurer un fonctionnement optimal des installations.
Cet article détailleles 8 piliers du TPM et explique comment leur mise en œuvre peut contribuer à la performance globale de votre entreprise.
Les 8 Piliers du TPM pour une Maintenance Optimale
1. Amélioration continue (Kaizen)
Le premier pilier du TPM consiste à mettre en place une culture d'amélioration continue.
Également connue sous le nom de démarche Kaizen, l’amélioration continue est un pilier essentiel de la Maintenance Productive Totale (TPM).
La démarche consiste à rechercher en permanence des moyens d'améliorer les processus, les performances et la qualité des produits, en adoptant une approche proactive et collaborative.
Le Kaizen implique de réunir les employés de tous les niveaux hiérarchiques pour identifier les problèmes, proposer des solutions innovantes et mettre en œuvre des actions correctives. Cette méthode permet d'optimiser la gestion des équipements, de réduire les temps d'arrêt, d'améliorer la qualité et de renforcer l'efficacité des processus de production. En intégrant l'amélioration continue au sein de la TPM, les entreprises peuvent bénéficier d'une plus grande flexibilité, d'une meilleure adaptabilité aux changements et d'une compétitivité accrue sur le marché.
En choisissant une application collaborative afin de suivre votre tâche de maintenance, vous serez en mesure de créer et suivre des plans d’actions en temps réel. Ces données vous permettront de mettre en place une culture d’amélioration continue en impliquant un maximum des personnes concernées.
2. Maintenance autonome
La maintenance autonome est un élément clé de la Maintenance Productive Totale (TPM) qui vise à responsabiliser et impliquer les opérateurs dans la gestion de leurs équipements.
Cette approche consiste à former les opérateurs aux tâches de maintenance de base, telles que le nettoyage, la lubrification, l'inspection et le contrôle des machines.
En développant les compétences des opérateurs, la maintenance autonome permet de détecter et de résoudre rapidement les problèmes, ce qui contribue à prévenir les pannes et à réduire les temps d'arrêt.
Les bénéfices de la maintenance autonome pour la TPM incluent l'amélioration de la disponibilité et de la fiabilité des équipements, la réduction des coûts de maintenance, l'accroissement de la productivité et la promotion d'un environnement de travail collaboratif.
En impliquant activement les opérateurs dans la maintenance de leurs machines, la maintenance autonome favorise un engagement accru envers la qualité et la performance globale de l'entreprise. Les habilitations de vos opérateurs font partie intégrante de la stratégie de maintenance autonome à mettre en place.
L'importance des habilitations dans la maintenance autonome réside dans la nécessité de garantir que les opérateurs disposent des compétences, des connaissances et des autorisations requises pour effectuer les tâches de maintenance sur leurs équipements. Les habilitations permettent de s'assurer que les opérateurs sont aptes à mener les interventions de maintenance en toute sécurité, conformément aux procédures et aux normes établies.
L'octroi d'habilitations spécifiques aux opérateurs contribue à plusieurs aspects clés de la maintenance autonome :
- Sécurité : Les habilitations garantissent que les opérateurs connaissent les risques potentiels liés aux interventions de maintenance et qu'ils sont formés pour les éviter ou les atténuer. Ceci permet de réduire le risque d'accidents et d'assurer la sécurité des employés.
- Efficacité : Les opérateurs habilités sont mieux équipés pour détecter les problèmes et les résoudre rapidement, ce qui permet de réduire les temps d'arrêt et améliore la disponibilité des équipements.
- Qualité : Les habilitations garantissent que les opérateurs sont compétents pour effectuer les tâches de maintenance conformément aux normes de qualité requises, ce qui contribue à maintenir et à améliorer la qualité.
- Responsabilisation : Les habilitations renforcent le sentiment de responsabilité des opérateurs envers la performance et la maintenance de leurs équipements puisque les personnes habilitées sont les seules à pouvoir intervenir sur certaines interventions.
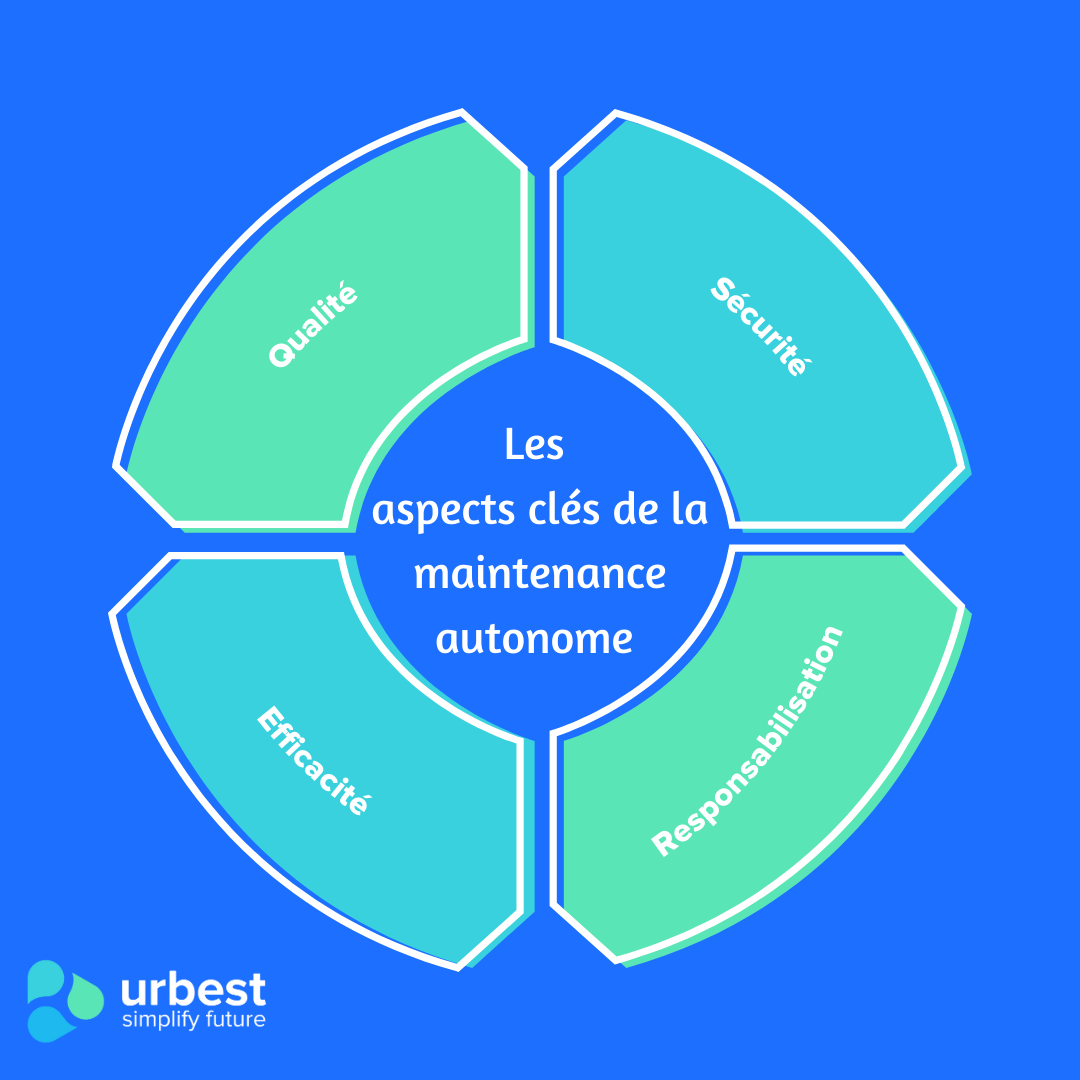
En somme, les habilitations jouent un rôle essentiel dans la maintenance autonome en garantissant que les opérateurs sont formés, compétents et autorisés à effectuer les tâches de maintenance requises. Cela permet d'assurer la sécurité, l'efficacité et la qualité des interventions, tout en renforçant l'engagement des opérateurs envers la performance de l'entreprise. Mis en pratique de façon digitale, cela revient à avoir au moins responsable par tâche de façon à éviter les “trous dans la raquette”.
3. Maintenance preventive
La maintenance préventive est un pilier central de la Maintenance Productive Totale (TPM) qui consiste à établir un programme de maintenance préventive pour chaque équipement. L'objectif de cette démarche est de minimiser les risques de panne et d'assurer un fonctionnement optimal des machines en planifiant et en réalisant régulièrement des interventions de maintenance. Les bénéfices de la maintenance préventive pour la TPM sont multiples :
- Réduction des coûts de maintenance : La maintenance préventive permet d'identifier et de résoudre les problèmes avant qu'ils ne causent des pannes majeures, ce qui réduit les coûts associés aux réparations d'urgence et aux temps d'arrêt prolongés. En principe, le fait de maitriser le calendrier des interventions permet de payer moins cher des tâches planifiées que des interventions en urgence parfois le soir ou le weekend.
- Amélioration de la disponibilité des équipements : Grâce à la planification et à l'exécution régulières des interventions de maintenance, les équipements sont maintenus en bon état de fonctionnement, ce qui augmente leur disponibilité et réduit les temps d'arrêt.
- Prolongation de la durée de vie des équipements : La maintenance préventive contribue à préserver les équipements et à prolonger leur durée de vie en assurant leur bon état et en évitant les défaillances prématurées.
- Optimisation de la performance des machines : En maintenant les équipements en bon état de fonctionnement, la maintenance préventive permet d'optimiser leur performance et d'améliorer la productivité globale.
- Amélioration de la sécurité et de la qualité : La maintenance préventive permet de détecter et de corriger les problèmes potentiels qui pourraient affecter la sécurité des opérateurs ou la qualité des produits, contribuant ainsi à la réduction des risques et à la satisfaction des clients.
Une application collaborative comme Urbest, vous permet de mettre en place facilement un plan de maintenance préventive en listant les tâches à faire avec des fréquences flexibles.
En effet, les tâches planifiées programmable depuis l’application ou à l’aide d’import Excel vous permettent de définir une récurrence et d’affecter directement l’intervention aux opérateurs concernés.
Les check-lists permettent également de structurervos vérification périodique et réglementaire.
En résumé, la maintenance préventive est un élément essentiel de la Maintenance Productive Totale (TPM), qui permet de réduire les coûts de maintenance, d'améliorer la disponibilité et la performance des équipements, de prolonger leur durée de vie, et d'assurer la sécurité et la qualité des processus de production. Pensez à utiliser les bons outils afin de mettre en place un plan de maintenance préventive efficace et répondant à toutes vos attentes.
4. La méthode AMDEC
La méthode AMDEC (Analyse des Modes de Défaillance, de leurs Effets et de leur Criticité) est un outil d'analyse systématique utilisé pour identifier et évaluer les risques potentiels associés à un processus, un produit ou un système. Cette approche contribue à la Maintenance Productive Totale (TPM) en aidant les entreprises à quantifier les risques à travers une approche triple : gravité, risque d'occurrence et risque de non détection. Les bénéfices de la méthode AMDEC pour la TPM sont nombreux :
- Identification des défaillances potentielles : L'AMDEC permet de détecter les modes de défaillance possibles des équipements, en analysant les causes et les conséquences de chaque défaillance sur la performance, la qualité et la sécurité.
- Priorisation des actions de maintenance : Grâce à l'évaluation de la criticité des défaillances et leurs probabilités de survenir, l'AMDEC aide à déterminer les actions de maintenance les plus importantes et priorise les ressources pour remédier aux problèmes les plus critiques.
- Amélioration de la fiabilité des équipements : En identifiant et en résolvant les problèmes potentiels, l'AMDEC contribue à augmenter la fiabilité des équipements, en réduisant les risques de pannes et les temps d'arrêt.
- Optimisation de la maintenance préventive : La méthode AMDEC permet d'ajuster les plans de maintenance préventive en fonction des risques identifiés, en ciblant les interventions sur les équipements les plus critiques et en évitant les opérations de maintenance inutiles.
- Amélioration de la sécurité et de la qualité : En identifiant les défaillances susceptibles d'affecter la sécurité des opérateurs et la qualité des produits, l'AMDEC permet de mettre en place des mesures préventives pour minimiser les risques et garantir la satisfaction des clients.
En conclusion, la méthode AMDEC est un outil précieux pour la Maintenance Productive Totale (TPM) qui permet d'identifier les défaillances potentielles, de prioriser les actions de maintenance, d'améliorer la fiabilité des équipements, d'optimiser la maintenance préventive et d'assurer la sécurité et la qualité des processus de production. C’est un moyen de se concentrer sur les tâches les plus critiques sous contraintes d’un budget en se concentrant sur l’essentiel.
5. La méthode 5S
La méthode 5S est une approche de gestion de l'environnement de travail basée sur cinq principes japonais : Seiri (trier), Seiton (ranger), Seiso (nettoyer), Seiketsu (standardiser) et Shitsuke (maintenir). Cette méthode vise à améliorer l'efficacité, la productivité et la sécurité en créant et en maintenant un espace de travail organisé et propre.
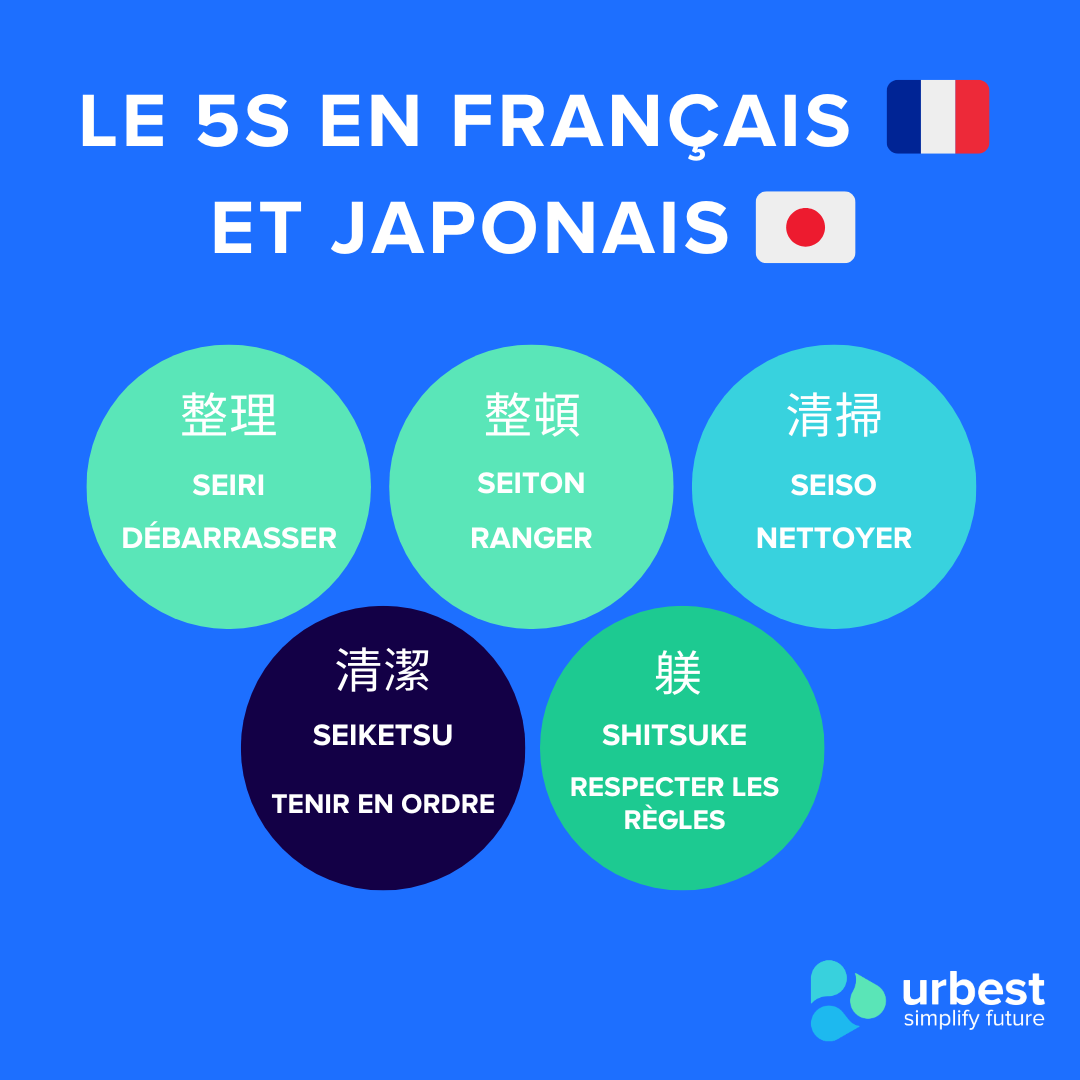
La méthode 5S apporte plusieurs bénéfices pour la Maintenance Productive Totale (TPM) :
- Amélioration de l'efficacité : En optimisant l'organisation de l'espace de travail et en facilitant l'accès aux outils, équipements et informations nécessaires, la méthode 5S permet aux opérateurs de réaliser leurs tâches de maintenance plus rapidement et efficacement.
- Réduction des temps d'arrêt : Un environnement de travail bien organisé et propre permet de détecter plus facilement les problèmes, tels que les fuites ou les dysfonctionnements, ce qui contribue à réduire les temps d'arrêt et à améliorer la disponibilité des équipements.
- Amélioration de la sécurité : En maintenant un espace de travail propre et dégagé, la méthode 5S contribue à réduire les risques d'accidents et de blessures, en éliminant les obstacles et les dangers potentiels pour les opérateurs.
- Standardisation des processus : La méthode 5S facilite la standardisation des procédures de maintenance, en établissant des routines claires et en s'assurant que les opérateurs suivent les meilleures pratiques.
- Renforcement de la culture d'amélioration continue : La mise en œuvre et le maintien des principes 5S encouragent les opérateurs à participer activement à l'amélioration de leur environnement de travail, ce qui favorise une culture d'amélioration continue et de responsabilisation.
En résumé, la méthode 5S est un outil précieux pour la Maintenance Productive Totale (TPM) qui permet d'améliorer l'efficacité, la sécurité et la productivité des opérations de maintenance, tout en renforçant la culture d'amélioration continue et la responsabilisation des opérateurs.
6. Maintenance prédictive
La maintenance prédictive est une approche avancée de la Maintenance Productive Totale (TPM) qui se base sur l'analyse des données et des tendances pour anticiper les défaillances potentielles des équipements.
Grâce à l'utilisation de capteurs IoT, de systèmes de surveillance et d'outils de ticketing et d'analyse de données, la maintenance prédictive permet de détecter les signes précurseurs d'un dysfonctionnement et de planifier les interventions de maintenance en conséquence. Les bénéfices de la maintenance prédictive pour la TPM sont nombreux :
- Optimisation des interventions de maintenance : La maintenance prédictive permet de planifier les opérations de maintenance en fonction des besoins réels des équipements, ce qui évite les interventions inutiles et optimise l'utilisation des ressources en décalant des interventions qui ne sont pas nécessaires tout de suite.
- Réduction des temps d'arrêt : En anticipant les défaillances et en planifiant les interventions de maintenance avant qu'une panne ne survienne, la maintenance prédictive contribue à minimiser les temps d'arrêt et améliore la disponibilité des équipements.
- Diminution des coûts de maintenance : La maintenance prédictive permet de réduire les coûts de maintenance en évitant les réparations d'urgence et les défaillances majeures, ainsi qu'en optimisant la gestion des pièces de rechange et des ressources humaines.
- Amélioration de la performance et de la durée de vie des équipements : La maintenance prédictive contribue à maintenir les équipements en bon état de fonctionnement et à prolonger leur durée de vie en détectant et en résolvant les problèmes avant qu'ils ne causent des défaillances.
- Amélioration de la sécurité et de la qualité : En identifiant et en résolvant les problèmes potentiels avant qu'ils n'affectent la sécurité des opérateurs ou la qualité des produits, la maintenance prédictive contribue à minimiser les risques et à garantir la satisfaction des clients.
En résumé, la maintenance prédictive est une méthode efficace de la Maintenance Productive Totale (TPM) qui permet d'optimiser les interventions de maintenance, de réduire les temps d'arrêt et les coûts, d'améliorer la performance et la durée de vie des équipements, ainsi que d'assurer la sécurité et la qualité des processus de production.
7. Le suivi de la performance
Le suivi de la performance du projet est essentiel pour assurer la réussite de la Maintenance Productive Totale (TPM) et pour mesurer l'efficacité des différentes actions mises en place. Plusieurs aspects sont à considérer dans le suivi de la performance :
- Les indicateurs : Il est important de définir des indicateurs clés de performance (KPI) pour mesurer l'efficacité de la TPM, tels que le taux de disponibilité des équipements, le coût de maintenance ou le nombre de pannes évitées.
- La communication : Une communication fluide et transparente entre les différents acteurs du projet est primordiale pour assurer la cohésion de l'équipe et faciliter la mise en œuvre des actions de TPM.
- La motivation : Encourager la participation active des opérateurs et les impliquer dans l'amélioration continue est essentiel pour maintenir leur motivation et favoriser la réussite de la TPM.
- Le pilotage de la fonction maintenance : La gestion efficace de la fonction maintenance, notamment à travers la planification, la coordination et le suivi des interventions, est cruciale pour atteindre les objectifs de la TPM.
- Le MTBF (Mean Time Between Failures) : Cet indicateur mesure le temps moyen entre deux pannes consécutives et permet d'évaluer la fiabilité des équipements. Une augmentation du MTBF indique une amélioration de la fiabilité des machines.
- Le MTTR (Mean Time to Repair) : Cet indicateur mesure le temps moyen nécessaire pour réparer un équipement en panne. Un MTTR réduit signifie une amélioration de l'efficacité de la maintenance et une réduction des temps d'arrêt.
8. Sécurité, santé et environnement
Le dernier pilier du TPM concerne la sécurité, la santé et l'environnement. Il s'agit de mettre en place des procédures et des pratiques de travail sécuritaires pour protéger les employés et l'environnement, tout en assurant la conformité avec les réglementations en vigueur. Ce pilier vise également à réduire les impacts environnementaux des activités de production, comme la consommation d'énergie et les émissions de gaz à effet de serre.
Conclusion : Les Avantages de la mise en place des 8 piliers du TPM
En appliquant les 8 piliers du TPM dans votre entreprise, vous pourrez bénéficier d'une série d'avantages qui contribueront à améliorer la performance globale de vos processus de production. Parmi les principaux avantages, on peut citer :
- Une meilleure disponibilité et fiabilité des équipements
- Une réduction des coûts de maintenance
- Une amélioration de la qualité des produits
- Une meilleure efficacité énergétique et un moindre impact environnemental
- Une amélioration de la sécurité et du bien-être des employés
En mettant en œuvre les 8 piliers du TPM, votre entreprise sera en mesure de se démarquer de la concurrence et d'assurer une croissance durable, tout en offrant des produits et des services de qualité à vos clients.