What is the "First Time Fix Rate" and how can it be improved?
In the highly competitive environment of maintenance management, even the smallest error can make a difference and customers want a fast service. As soon as a problem is identified on a piece of equipment, it has to be solved as quickly as possible and at the first visit.
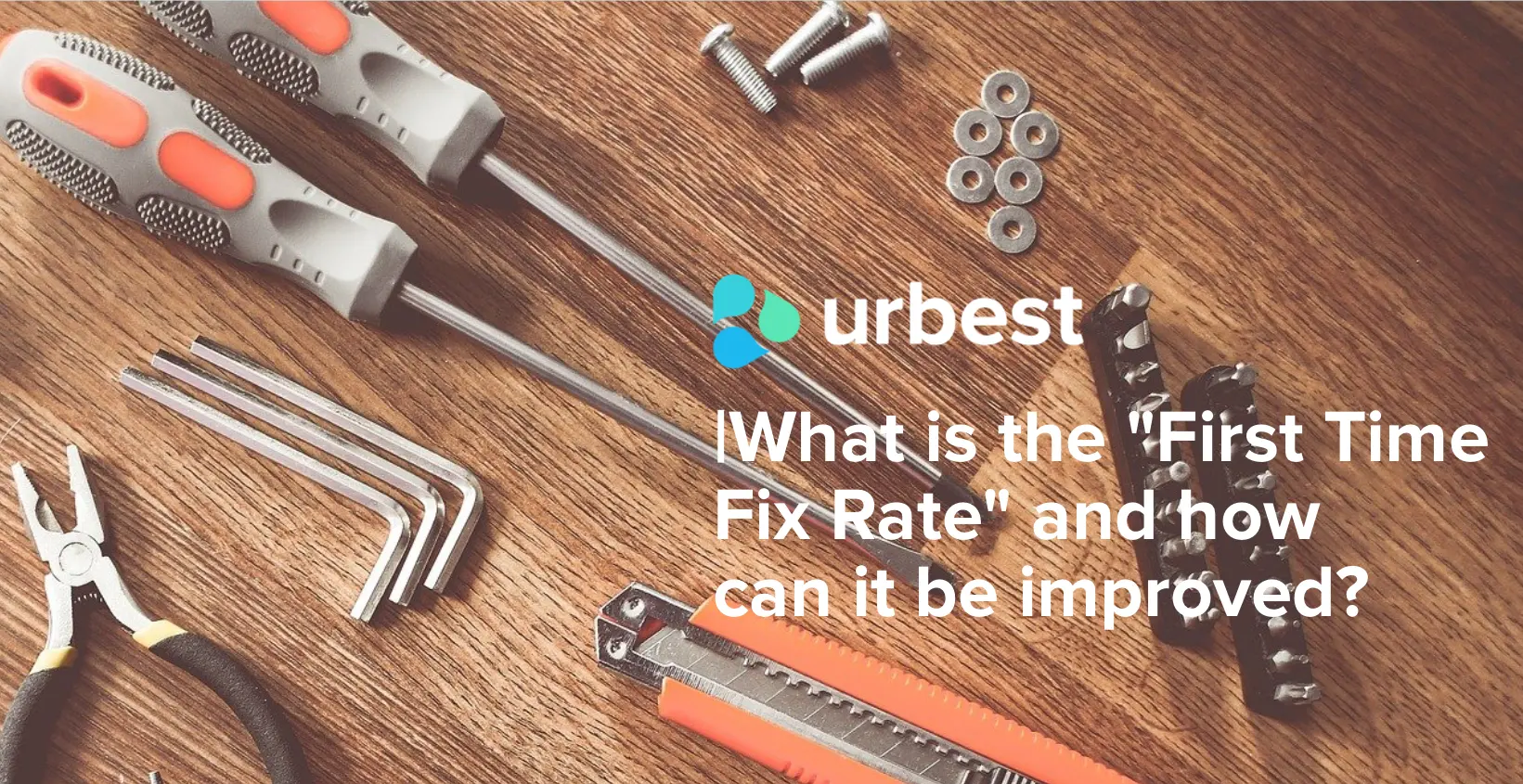
In the highly competitive environment of maintenance management, even the smallest error can make a difference and customers want a fast service. As soon as a problem is identified on a piece of equipment, it has to be solved as quickly as possible and at the first visit.
This will make the difference between a satisfied customer and an unhappy one, between customer retention and going out of business.
The "First Time Fix Rate" remains an important issue for all service and maintenance companies. In addition to customer satisfaction, multiple jobs/tasks can also increase your operating costs and put your business at risk.
First Time Fix Rate (FTFR) indicates the percentage of time a technician is able to fix the issue the first time, without need for additional expertise, information or parts.
According to a survey conducted by Akio in partnership with LSA, 70% of individuals say they are ready to change suppliers/brands if they do not get a satisfactory response from the first contact. Moreover, getting a clear and adapted answer from the first contact is important for 99% of them. These figures clearly highlight the importance of good customer service within a company, as the risk of losing customers remains high.
As we move forward, in this article we will give you some tips on how to improve your First Time Fix Rate (FTFR).
1 - Monitor job/issue requests
In order to process your jobs/issues quickly and efficiently, the first step is to identify them correctly. Indeed, a poorly documented problem will subsequently create difficulties for you to intervene on.
Digital solutions will enable you to manage this important phase of information gathering efficiently. Software such as Urbest, which can be used by both you and your clients, will remedy this type of difficulty thanks to its simple and intuitive interface. It will allow you to identify and detail your issues by taking into account the following points:
- The location of the issue
- The type of issue
- The person in charge of the issue
- Photos/Files attached to the problem
Furthermore, the instantaneous nature of the process will allow you and the person in charge of the resolution to be aware of the problem very quickly. As the application is available on mobile, your technicians will have all the information in real time and will be able to communicate with you or your customer through the tool. This will certainly improve your reactivity, your quality of service and thus the satisfaction of your customers. On your side, a software for the resolution of issues put in the hands of your customer can save you the hassle of having a call centre and thus improve your margins.
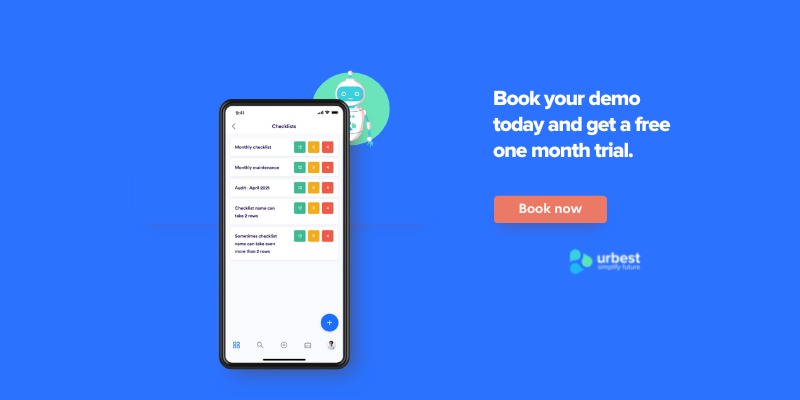
2 - Planning your operations
Good management of the planning of your tasks should also be an operational priority for your company. For this phase too, a mobile application will be able to help you, as excel spreadsheets do not allow for planning, whereas a SaaS tool such as Urbest will do the trick.
In addition to the details of the task, the platform integrates a calendar and the possibility of setting deadlines (or due dates) for the resolution of these tasks. All these features are designed to enable your technicians in the field to carry their duties quickly and efficiently.
At the end of the job and thanks to the data analysis provided by the tool, you will have all the necessary KPI's in order to set up a maintenance strategy adapted to your site or customer in the case of a maintenance contract.
3 - Predictive maintenance
Predictive maintenance consists of anticipating future failures in equipment, objects, systems, etc. In concrete terms, it involves anticipating a breakdown or malfunction thanks to the accumulation of a set of data.
The aim of this type of maintenance is to act on potential failures as they approach a period of malfunction. It also makes it possible to monitor deterioration in the case of a variable life of an equipment. All these actions therefore make it possible to reduce the frequency of breakdowns while optimising the frequency of preventive jobs done.
To implement predictive maintenance, it is necessary to
- List the elements to be monitored,
- Know or find the monitoring method to be applied,
- Check the possibility of implementing this system,
- Establish the alert threshold(s),
- Decide on the alert method,
- Establish the frequency of reporting,
- Introduce the procedure into the preventive maintenance plan.
Preventive maintenance aims to maintain the equipment on the assumption that it will fail within a certain time; the equipment will be replaced or repaired before it fails.
Predictive maintenance, on the other hand, is more intelligent: it monitors trends that predict possible failures in your systems to prevent them from occurring. In this way, you optimise the safety of your environment, and ensure that your operations run smoothly.
Predictive maintenance has the advantage of spacing out tasks over time and ultimately lowering the cost of preventive maintenance.
By moving from corrective maintenance to predictive maintenance, the first-time resolution rate will increase considerably, and the level of customer satisfaction will follow the same trend.
In conclusion, as customers become more demanding and used to quick feedback loops, you will need to adapt to this evolution. It is no longer enough to send a technician on site quickly.
Your objective will be to bring him your support and tools so that the problems are solved from the first visit
To know more about maintenance strategies:
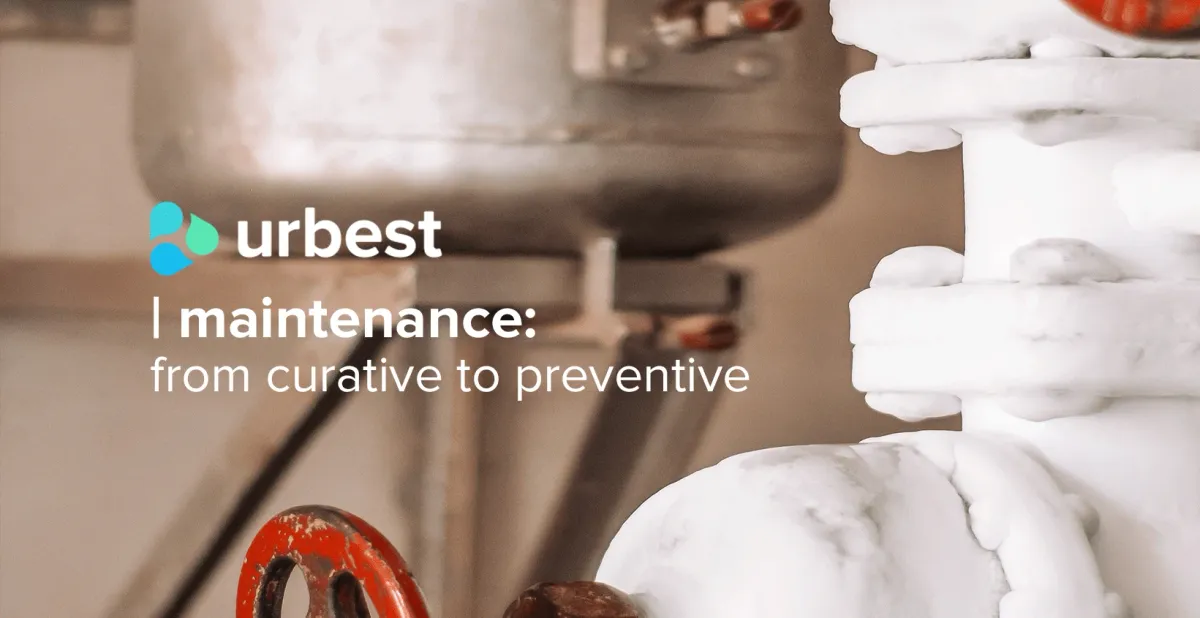
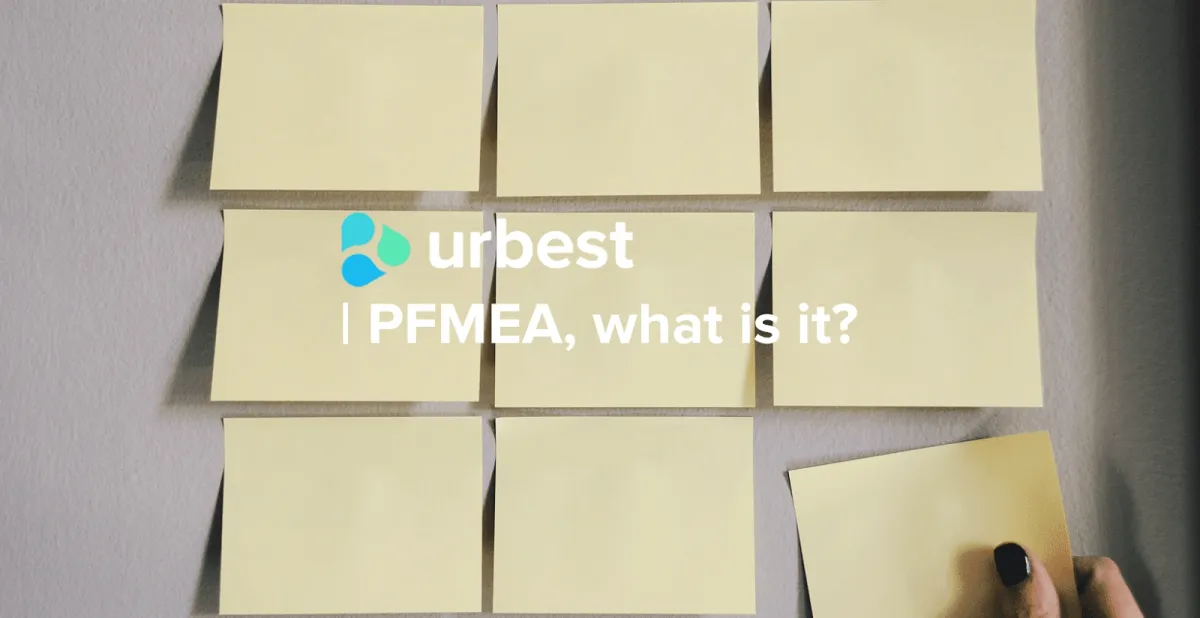